Circular Industrial Cutting Blades: A Comprehensive Guide
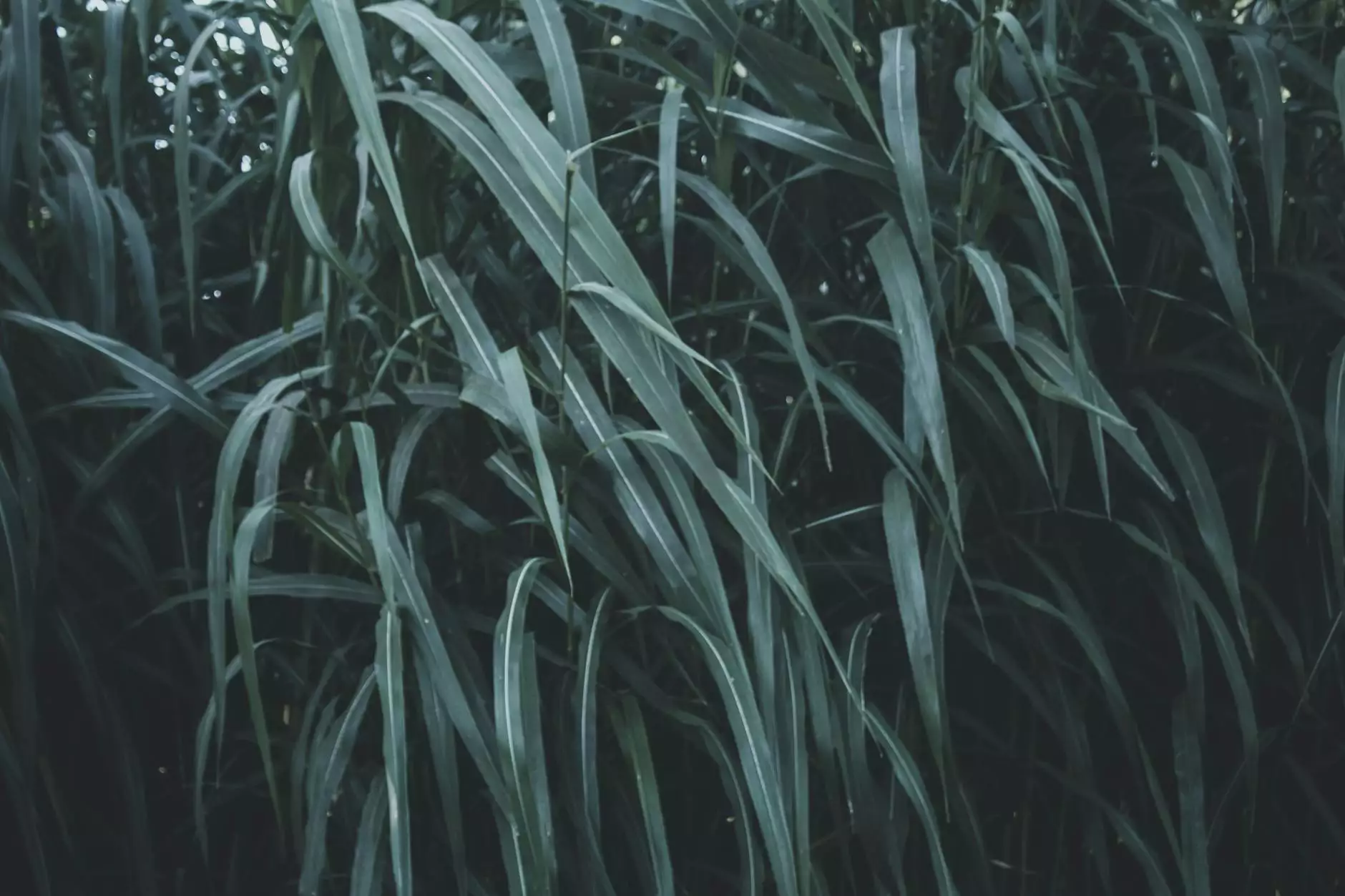
The circular industrial cutting blades are a cornerstone in various manufacturing and industrial sectors. Their precision and efficiency make them essential tools for cutting, slicing, and trimming materials into desired shapes and sizes. In this article, we'll delve deeply into the nuances of these powerful tools, covering everything from their design to their applications, maintenance, and benefits.
Understanding Circular Industrial Cutting Blades
Circular industrial cutting blades are engineered tools predominantly used in industries that require high-volume and accurate cutting. From wood and metal to plastics and textiles, these blades are designed to offer supreme cutting performance while maintaining safety and minimizing waste.
What Are Circular Cutting Blades?
At their core, circular cutting blades are round tools with a sharp edge utilized to cut through various materials. They are installed on machines, such as saws or lathes, and rotate at high speeds to perform accurate cuts. Depending on the application, these blades can have varied diameters, thicknesses, and tooth configurations.
Types of Circular Industrial Cutting Blades
There are several types of circular industrial cutting blades, each specifically designed for particular materials and applications:
- Wood Cutting Blades: Designed with fewer teeth and wider gullets, ideal for fast cuts in lumber and engineered wood.
- Metal Cutting Blades: These have high tooth counts and are constructed from durable materials like carbide or bi-metal for cutting metals.
- Plastic Cutting Blades: Optimized for cutting plastic materials, providing clean cuts without melting or warping.
- Textile Cutting Blades: Fine-toothed blades designed for precision cuts in fabrics and textiles.
Key Features of Quality Circular Industrial Cutting Blades
When choosing circular industrial cutting blades, there are several key features to consider:
- Material Composition: Blades made from high-speed steel, carbide-tipped, or diamond-coated materials provide better durability and performance.
- Tooth Geometry: The tooth shape and configuration affect the type of cut and material suitability. Raker, flat, and alternate tooth geometries cater to different cutting needs.
- Thickness and Diameter: The thickness of the blade impacts its strength and the type of machine it can be used with, while the diameter determines the size of the cut.
- Blade Coating: Coatings can enhance the lifespan, reduce friction, and prevent buildup from cutting materials.
Benefits of Using Circular Industrial Cutting Blades
The advantages of employing circular industrial cutting blades are manifold:
1. Precision and Efficiency
Circular blades provide precise cuts, allowing industries to achieve exact dimensions in their products. This level of accuracy reduces waste and boosts overall efficiency in production processes.
2. Versatility
These blades can cut through a variety of materials with the right specifications, making them incredibly versatile tools in both small and large-scale operations.
3. Cost-Effectiveness
With proper maintenance, circular cutting blades can be reused multiple times. This longevity reduces the overall cost per cut in manufacturing processes, offering businesses a more economical solution.
Choosing the Right Circular Industrial Cutting Blade
Selecting the appropriate circular industrial cutting blade involves considering multiple factors:
- Material Specifications: Identify the material that needs to be cut and the thickness to determine the best blade type.
- Machine Compatibility: Ensure that the blade is compatible with the cutting machine regarding size and RPM (revolutions per minute).
- Application Needs: Consider whether the cuts need to be smooth (e.g., for woodworking) or rough (e.g., for demolition).
Maintenance Tips for Circular Industrial Cutting Blades
Proper maintenance can enhance the lifespan and cutting performance of these blades. Here are essential maintenance tips:
1. Regular Inspection
Examine the blades frequently for signs of wear, damage, or dullness. Early detection can prevent costly repairs or replacements.
2. Sharpening
Regular sharpening is crucial to maintaining cutting efficiency. A dull blade can increase production time and diminish cut quality. Knife sharpening services, like those provided at szblade.com, can help keep your blades in optimal condition.
3. Cleaning
Post-use cleaning is essential to remove residue and debris. Keeping the blades clean reduces friction and prolongs their sharpness.
4. Correct Storage
Store blades in a dry environment, away from moisture and direct sunlight. Utilize blade protectors or sheaths to prevent physical damage during storage.
Applications of Circular Industrial Cutting Blades
Circular cutting blades find their applications across numerous industries. Here are some notable examples:
1. Woodworking
In the woodworking industry, circular blades are integral for cutting timber, plywood, and engineered woods. They allow for clean and exact cuts that are critical for furniture making, cabinetry, and flooring.
2. Metal Fabrication
Metal cutting blades are indispensable in machining and fabrication. These blades slice through metals with precision, essential for automotive, aerospace, and construction applications.
3. Plastics Manufacturing
Plastic industries rely on specially designed blades to achieve flawless cuts in various plastic forms, ensuring product integrity and appearance.
4. Textile Production
In textile and apparel manufacturing, circular blades are utilized for cutting fabrics efficiently, ensuring raw materials are utilized effectively with minimal waste.
The Future of Circular Industrial Cutting Blades
The future of circular industrial cutting blades is poised for innovation. Advancements in materials science, manufacturing technologies, and automation are reshaping the blade industry. The utilization of AI and machine learning for predictive maintenance and blade optimization could soon revolutionize how businesses manage cutting processes, leading to greater efficiency and productivity.
Innovative Technologies
Emerging technologies like laser cutting, water jet cutting, and CNC (Computer Numerical Control) cutting systems integrate the utility of circular blades in novel ways, expanding their applications across industries.
Sustainability Considerations
As industries move toward more sustainable practices, the demand for environmentally friendly cutting solutions will rise. Innovations in blade recycling and the use of sustainable materials for manufacturing cutting blades are key trends to watch.
Conclusion
Circular industrial cutting blades are indispensable tools that drive efficiency and precision across various sectors. By understanding their types, features, and maintenance, businesses can select the right blades to optimize performance. As industries evolve, staying vigilant about advancements will ensure that your operations remain competitive in an ever-changing market. For more information and high-quality solutions, visit szblade.com.