LEV Installation in South Wales: Ensuring a Safer Environment for Your Business
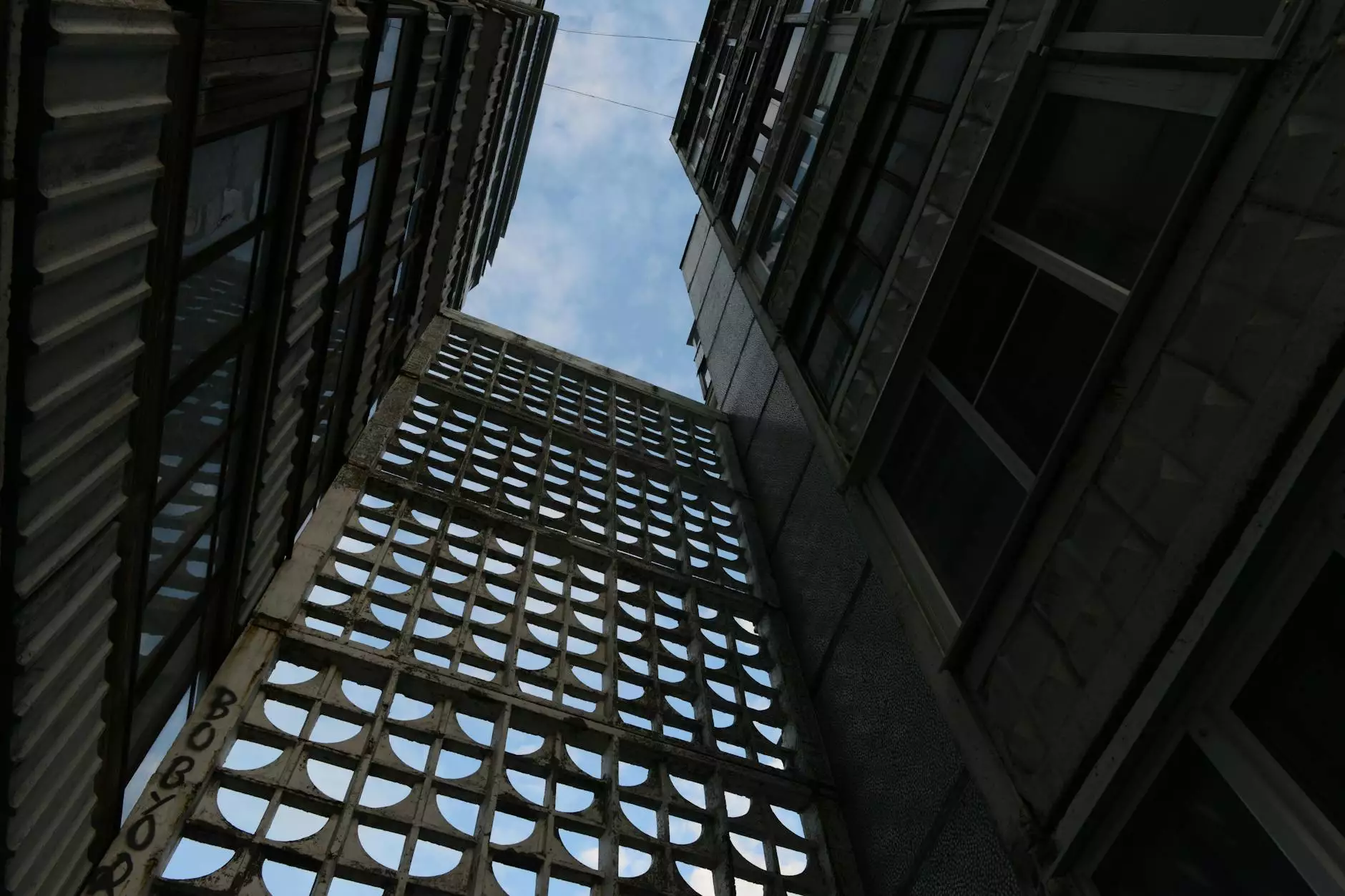
When it comes to maintaining a healthy and safe working environment, Local Exhaust Ventilation (LEV) systems play a pivotal role in many industries. In South Wales, businesses of all sizes are increasingly recognizing the importance of LEV installation. This necessary measure not only enhances workplace safety but also adheres to regulatory standards set forth by health and safety authorities. In this article, we will delve deeply into the significance of LEV systems, the installation process, and their benefits in a variety of sectors including Home & Garden, Gardening, and Pest Control. Let’s explore why choosing LEV installation in South Wales is essential for your business operations.
Understanding LEV Systems
LEV systems are designed to capture and filter harmful airborne contaminants at their source before they spread into the workspace. These systems are essential for industries such as woodworking, metalworking, manufacturing, and even agricultural sectors. Understanding how these systems function can help businesses comprehend their value and implementation needs.
How LEV Systems Work
The mechanics of an LEV system involve several key components, including:
- Capture Hood: This is positioned close to the source of the contaminant. It’s designed to capture contaminants effectively before they disperse into the air.
- Ductwork: The contaminated air is transported through a network of ducts designed to minimize air resistance and maintain airflow.
- Filter Unit: This section cleans the air by removing pollutants before it is released back into the atmosphere.
- Exhaust Vent: The cleaned air is then expelled safely outside to prevent re-circulation of harmful substances.
Why Invest in LEV Installation in South Wales?
Investing in LEV installation for your business is not just about compliance – it's about creating a sustainable working environment. Here are some compelling reasons to consider:
1. Enhanced Workplace Safety
One of the primary benefits of LEV systems is their capability to protect workers from inhaling hazardous substances. By aligning with Health and Safety Executive (HSE) guidelines, businesses can ensure their workers are not exposed to excessive levels of pollutants.
2. Improved Staff Productivity
When workers are provided with a clean and safe environment, their productivity naturally increases. Reduced risks of respiratory issues and other health problems lead to fewer sick days and a more focused workforce.
3. Regulatory Compliance
South Wales businesses must adhere to strict health and safety regulations. Implementing a robust LEV system ensures compliance and helps avoid potential fines or penalties associated with neglecting occupational safety standards.
4. Cost Savings
Though the initial investment in LEV installation can be considerable, the long-term savings on healthcare costs and increased productivity often outweigh these costs. Ensuring a healthy workforce mitigates risks and reduces liability.
Choosing the Right LEV System for Your Business
With a myriad of options available, selecting the appropriate LEV system is critical for maximizing its effectiveness. Consideration factors include:
- Type of Contaminants: Understanding what types of pollutants your workspace generates will guide the selection of appropriate capture methods and filter types.
- Workspace Layout: Evaluating the layout of your facility can impact the design of the ductwork, positioning of capture hoods, and overall efficiency of the LEV system.
- Volume of Airflow: Assessing the required airflow rates and ensuring sufficient ventilation is crucial for maintaining a safe environment.
- Maintenance Needs: Choose a system that can be maintained easily without disrupting your business operations.
The Installation Process of LEV Systems
Installing an LEV system is a systematic process that should be executed by qualified professionals. Here’s an overview of the key steps involved in this process:
1. Consultation and Assessment
The first step involves assessing your business needs and workspace to identify potential hazards and the type of LEV system required. This integral phase may involve a detailed inspection and conversations with management to understand specific operational challenges.
2. Designing the System
Once the assessment is complete, a custom system design will be developed. This includes designing the layout of ducts, determining the placement of capture hoods, and selecting suitable filtration units for your specific operational needs.
3. Installation
The actual installation is typically done in stages and may involve coordinating with various contractors, especially in larger facilities. Professionals will ensure that the installation meets all safety and health regulations.
4. Testing and Commissioning
After installation, the system must be thoroughly tested to verify its effectiveness in capturing and filtering contaminants. This testing ensures that the system operates within the required specifications and is ready for regular use.
5. Training and Documentation
Comprehensive training for staff on how to operate and maintain the system is also essential. Providing documentation such as maintenance schedules and operational manuals promotes long-term efficiency.
Regular Maintenance of LEV Systems
For optimal performance of LEV systems, routine maintenance is essential. Here are some crucial aspects of maintaining your LEV installation:
- Regular Inspection: Schedule periodic inspections to identify any potential issues early on.
- Cleaning: Regular cleaning of filters and ducts is necessary to maintain airflow and efficiency.
- System Upgrades: Consider periodic upgrades to accommodate changes in your operational processes or to incorporate advancements in LEV technology.
Benefits Across Diverse Sectors
The implementation of LEV systems yields unique benefits across various industries, particularly in South Wales.
In the Home & Garden Sector
For businesses catering to home improvement and gardening, LEV systems help manage dust and chemical fumes generated from tools and treatments, safeguarding both employees and customers.
In Gardening Operations
In commercial gardening and landscaping services, LEV systems can effectively filter out pesticides and particulates, promoting a safer working environment for garden staff who frequently handle fertilizers and treatments.
In Pest Control Services
Pest control companies dealing with a variety of chemicals benefit remarkably from LEV installations, as they mitigate the risks associated with airborne toxins, ensuring that both technicians and clients remain safe during treatments.
Conclusion: Elevate Your Business with LEV Installation in South Wales
LEV installation is not merely an option but a necessity for businesses in South Wales that prioritize health and safety. With a customized approach tailored to your specific needs, investing in these systems enhances the quality of your working environment, boosts productivity, and ensures regulatory compliance. The long-term advantages clearly outweigh the initial investments, securing not only the health of your team but also the sustainability of your operations.
For professional and compliant LEV installation services in South Wales, consider enlisting expert services from safeplantuk.co.uk. They specialize in providing tailored solutions that cater to the unique requirements of various sectors, ensuring that your business thrives in a safe environment.
Embrace the future of workplace safety today with dedicated LEV installation, and watch as your business flourishes while maintaining a commitment to health and safety.
lev installation south wales