Unveiling the Importance of OEM Lathe Machining Parts Manufacturers
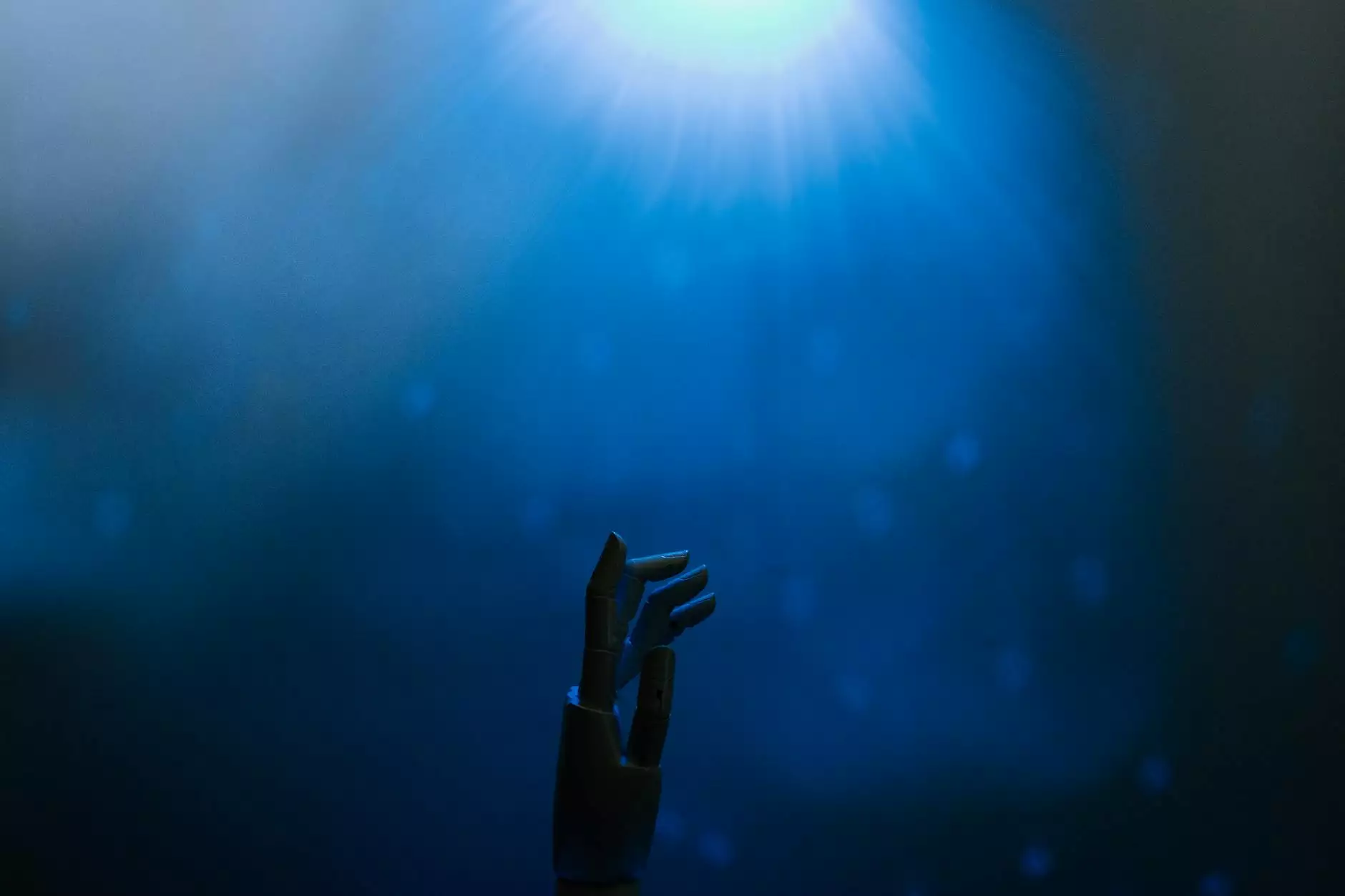
What are OEM Lathe Machining Parts?
The term OEM stands for Original Equipment Manufacturer. In the context of lathe machining, it refers to parts that are designed, manufactured, and supplied specifically for a manufacturer's original product. This means that OEM lathe machining parts are not only crucial for the functionality of machinery but also play a significant role in maintaining the integrity and quality of the products they serve.
The Role of an OEM Lathe Machining Parts Manufacturer
OEM lathe machining parts manufacturers are responsible for producing highly specialized components that meet exact specifications. These components are used across various industries, including automotive, aerospace, medical, and industrial machinery. The precision and quality of these parts can directly influence the performance and durability of the end products.
Choosing the right manufacturer is crucial, as it impacts not only the quality of the parts but also overall production timelines and cost efficiency. For companies like DeepMould.net, offering reliable and high-quality OEM lathe machining parts is essential for maintaining customer satisfaction and building long-term partnerships.
Key Benefits of Using OEM Lathe Machining Parts
There are several advantages to using components provided by an OEM lathe machining parts manufacturer:
- Precision Engineering: OEM manufacturers focus on creating parts that meet stringent tolerances and specifications, ensuring they fit perfectly into the intended application.
- Quality Assurance: Many OEM parts undergo rigorous testing and quality assurance processes to ensure they meet industry standards.
- Cost Efficiency: While OEM parts may seem higher in price initially, they often provide better long-term value due to their durability and reliability.
- Customization: Many OEM manufacturers, such as DeepMould.net, offer customization options, allowing for unique designs that cater to specific needs.
- Supply Chain Security: Partnering with a dedicated OEM manufacturer helps businesses streamline their supply chain, ensuring consistent delivery of quality parts.
Choosing the Right OEM Lathe Machining Parts Manufacturer
When selecting an OEM lathe machining parts manufacturer, consider the following criteria:
- Experience and Expertise: Look for manufacturers with a proven track record in the industry. DeepMould.net, for example, has years of experience and a strong reputation.
- Compliance with Standards: Ensure the manufacturer adheres to relevant industry standards and certifications, which reflect their commitment to quality.
- Technical Capabilities: Evaluate the technical capabilities of the manufacturer, including their machinery, technology, and skilled workforce.
- Customer Support: Reliable customer support can make a significant difference in your partnership. A manufacturer that communicates effectively is invaluable.
Metals Used in OEM Lathe Machining
OEM lathe machining can employ a variety of metals, each offering unique properties tailored to specific applications. Some commonly used metals include:
- Aluminum: Lightweight and resistant to corrosion, aluminum is ideal for applications requiring reduced weight without compromising strength.
- Steel: Known for its strength and ductility, steel is used in numerous applications, from automotive to industrial machinery.
- Brass: With excellent machinability and corrosion resistance, brass is often used in applications requiring good conductivity.
- Stainless Steel: This alloy is known for its excellent corrosion resistance and is widely used in medical and food processing applications.
The Process of OEM Lathe Machining
The process of producing OEM lathe machining parts involves several meticulous steps:
- Design: The process begins with detailed design and engineering, often using CAD software to create precise models of the components.
- Material Selection: Choosing the right material is crucial for ensuring the final part meets performance criteria.
- Machining: The lathe machining process utilizes various cutting tools and techniques to shape the material into the desired form.
- Finishing: After machining, parts often require additional finishing processes such as polishing, coating, or heat treatment to enhance performance.
- Quality Control: Rigorous testing and inspections are performed to ensure the parts meet quality and specification standards before delivery.
Industry Applications of OEM Lathe Machining Parts
OEM lathe machining parts are used in a wide range of industries:
- Automotive: From engine components to transmission parts, OEM lathe machining plays a vital role in vehicle manufacturing.
- Aerospace: In the aerospace sector, precision and reliability are paramount, making OEM parts essential for aircraft manufacturing.
- Medical: Surgical instruments and equipment often rely on precise OEM machining for functionality and safety.
- Industrial Machinery: Countless machines in manufacturing and production environments depend on high-quality OEM parts for optimal performance.
Innovations in OEM Lathe Machining
The landscape of OEM lathe machining is continually evolving, driven by innovations in technology and manufacturing processes. Some notable advancements include:
- Automation: Automation technologies such as CNC (Computer Numerical Control) machining have significantly enhanced precision and reduced production times.
- Advanced Materials: The development of new alloys and composites is expanding the range of applications for OEM lathe machining.
- 3D Printing: While traditional machining remains dominant, additive manufacturing is starting to play a role in creating complex geometries.
- IoT Integration: The integration of the Internet of Things (IoT) into manufacturing processes is allowing for real-time monitoring and optimization.
Conclusion
In conclusion, the importance of partnering with a reliable OEM lathe machining parts manufacturer like DeepMould.net cannot be overstated. Their commitment to quality, precision, and innovation ensures that businesses receive components tailored to their specific needs. As industries evolve and technologies advance, the role of OEM manufacturers will remain pivotal in shaping the future of precision machining.
By understanding the intricate details involved in the OEM lathe machining process and the benefits that come from using these high-quality parts, companies can make informed decisions that support their growth and operational efficiency.