Lifting Equipment LOLER Cardiff
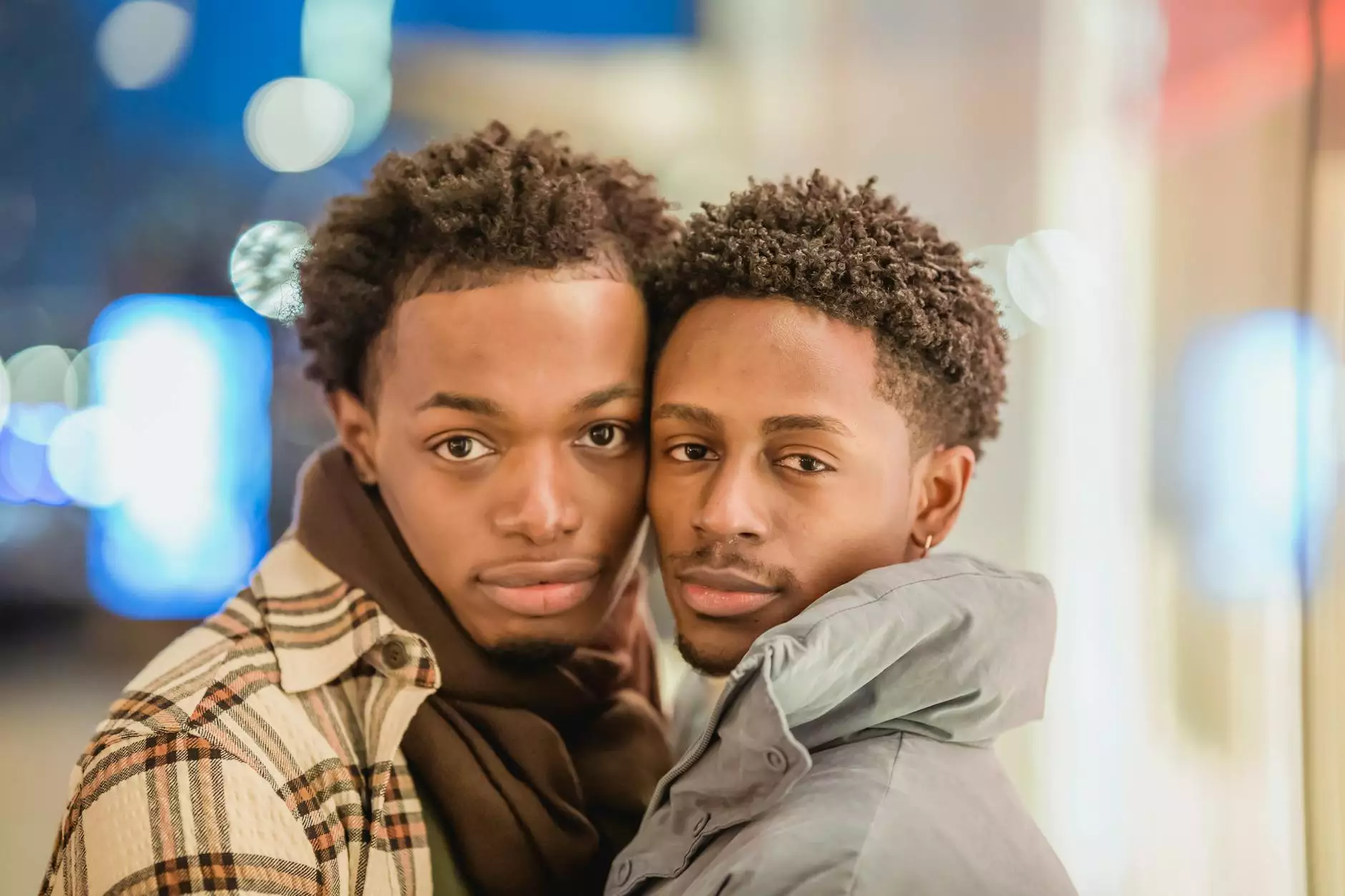
If you're operating lifting equipment in Cardiff, understanding the Lifting Operations and Lifting Equipment Regulations (LOLER) is crucial. This legislation helps ensure safety and compliance in the workplace. In this comprehensive guide, we will delve deeper into lifting equipment, its significance, the LOLER regulations, and how Safe Plant UK can assist your business in maintaining high safety standards.
Understanding Lifting Equipment
Lifting equipment refers to machinery and devices used to lift and lower loads, including cranes, hoists, and slings. This equipment is essential in various industries, including construction, manufacturing, and logistics. Proper use of lifting equipment is essential for:
- Worker Safety: Preventing accidents and injuries associated with lifting tasks.
- Operational Efficiency: Ensuring smooth and effective lifting operations that enhance productivity.
- Equipment Longevity: Reducing wear and tear on machinery through proper use and maintenance.
The Importance of LOLER Regulations
The LOLER regulations are integral to ensuring safe lifting operations. Enforced in the UK since 1998, these regulations require that lifting equipment is:
- Well Maintained: Equipment must be maintained in a safe condition and undergo regular inspections.
- Properly Tested: All lifting gear must be tested for strength and stability before use.
- Clearly Marked: Equipment should display clear information about its safe working load (SWL).
These regulations aim to minimize risk in the workplace, ensuring that employers adhere to robust guidelines that protect workers and business assets alike.
LOLER Compliance: What You Need to Know
Compliance with LOLER in Cardiff involves several key elements. Here’s what you should consider:
1. Regular Inspections and Testing
Your lifting equipment must undergo thorough inspections at regular intervals. This should be done by a competent person who can assess the condition of the equipment and ensure it meets safety standards. Inspections typically include:
- Visual checks for any damage or deterioration.
- Functionality tests to verify performance.
- Documentation of all findings and necessary recommendations.
2. Maintenance Practices
Implementing robust maintenance practices is vital. Maintenance should include:
- Scheduled maintenance: Regular servicing based on manufacturer recommendations.
- Immediate repairs: Addressing any problems as soon as they arise to avoid prolonged equipment downtime.
- Training staff: Ensuring operators know how to use lifting equipment correctly.
3. Documentation and Record Keeping
Maintaining accurate records of inspections, maintenance, and testing is not just good practice; it’s a legal requirement under LOLER. Your documentation should include:
- Results of all inspections and tests.
- Details of any faults found and corrective actions taken.
- Records of maintenance performed, including dates and the personnel involved.
How Safe Plant UK Helps You Navigate LOLER Regulations
Safe Plant UK is committed to ensuring your lifting operations are safe and compliant. Here’s how we contribute to your success:
Expert Knowledge and Guidance
Our team comprises experts in lifting equipment and LOLER regulations. We offer tailored consultancy services to help your business understand compliance requirements specific to Cardiff and beyond.
Lifting Equipment Inspection and Testing Services
We provide comprehensive equipment inspections and testing services to ensure your lifting equipment meets all safety regulations. Our skilled inspectors follow stringent protocols to assess the integrity and functionality of your lifting systems.
Training and Development Programs
Safe Plant UK offers training programs designed to equip your staff with the skills and knowledge necessary for safe lifting practices. Our training covers:
- Operating and maintaining lifting equipment.
- Recognizing hazards and ensuring safety measures are in place.
- Understanding LOLER regulations and their implications for your business.
Choosing the Right Lifting Equipment
Selecting the appropriate lifting equipment for your operations is critical. Factors to consider include:
Load Requirements
Understand the weight and type of loads you will be lifting. This affects your choice of equipment, impacting safety and effectiveness.
Type of Lifting Operation
Different operations require different equipment. For instance, a construction site may require a crane, while a warehouse may need a forklift. Assess your specific needs carefully.
Environmental Conditions
The conditions in which the equipment will be used also matter. Outdoor equipment may need to withstand weather conditions, whereas indoor lifting could focus on space optimization.
The Future of Lifting Equipment in Cardiff
The lifting equipment industry is evolving rapidly, with advancements in technology enhancing safety and efficiency. Smart lifting devices that provide real-time data on load safety and equipment status are becoming increasingly popular.
As regulations tighten and the push for compliance grows, understanding these trends will be essential for businesses in Cardiff. Educating yourself and investing in high-quality lifting equipment will pay dividends in the long run.
Conclusion
In summary, compliance with the LOLER regulations is not just about legality; it's about creating a safe work environment for everyone involved. Partnering with experts like Safe Plant UK ensures your lifting operations meet the highest standards, protecting your business and workforce.
For more information on lifting equipment LOLER Cardiff and how we can help you, visit our website at safeplantuk.co.uk.